Technical Informations / Line Pressure Test
PROCEDURE
Preliminary Test
- Line is filled with water. Air compression in the line is removed by opening the valve at the highest point during filling.
- Line is closed.
- Test pressure is determined with PN (operation pressure) + 5 bar or PN x 1.5 (whichever is low).
- Line is brought to test pressure with a suitable pump during 10 min.
- In order to fix the test pressure, pump is continued during 10 min.
- Pump is stopped. Distribution line is left as it is for 60 min.
- Piping line undergoes a visco-elastic deformation.
No pressure drops more than %30 should occur within 60 min. In both cases, test is ended. After observation and temperature control to be carried on the line, all tensions in the line are removed and then preliminary test is repeated.
Main Test
One of the below methods is applied in the main test.
Pressure Dropping Method :
- By the end of 60 min. the pressure of the line is dropped by values below.
Pipe | Normal Pressure | Pressure Dropping |
---|---|---|
HDPE | 10 | 2 |
HDPE | 16 | 3 |
HDPE | 10 | 2 |
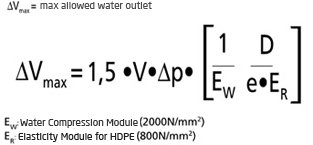
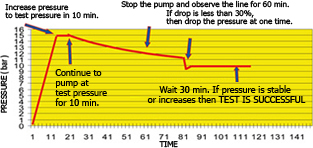
After pressure drop, contraction time is allowed for 30 min. If pressure is stable or increases for 30 min, line is accepted to be tight. In case of inconsistency, test duration is extended to 1.5 hour. However, during this duration, max 0.25 bar pressure drop is allowed. If pressure drop more than 0.25 bar is observed, then there is a leakage in the distribution line.
Water Volume Loss Method in Pressure Dropping :
- During pressure dropping, volume of the water comes out is determined. ( Vt )
- With AV max formulae, the max water volume that can come out line is calculated. If it is Vt V, then test is valid.
Note :In line test, temperature of the water filled in the pipe system and test ambient temperature is important. For conditions above 20 °C, pressure dropping coefficients depending on heat will be used. Test should not be conducted at above 40°C.